Solutions for fire prevention in the tissue paper conversion processes, with the highest technical standards and the latest technology.
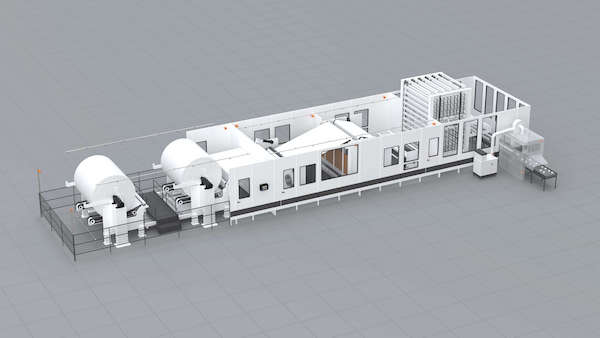
The converting process normally generates a lot of dust and other cellulose debris, which can rapidly ignite due to friction for example, in and around bearings especially when tissue stripes build in these areas. If the converting assets, such as an embosser, is enclosed, even more dust accumulates inside and the risk of fire increases. Traditional extinguishing systems, such as sprinklers, will not be able to reach these high-risk fire areas. Firefly, with Tissue Solutions®, offers a range of complete fire prevention and protection solutions, specially designed for both the tissue machine and the complete converting process.
Firefly launched and obtained the world’s first third party certified Quick Suppression System. It is a complete system designed for extremely quick detection and suppression of flames or fires in and around critical machinery and high-risk areas. The system aims to identify and extinguish the incident in seconds, typically less than 10 seconds, and the purpose is to act quick enough to avoid or significantly reduce damages and production downtime. Currently, Firefly has protected more than 200 sites on five continents where tissue paper is manufactured and converted.
Unwinding
The Unwinder area is considered high risk, and this is because:
- It generates a lot of dry dust that can accumulate on bearings, shafts and frames.
- A jumbo roll could contain a dangerous ignition source or dangerous particulate that when unwinding could have access to oxygen and start a fire in the process.
- Shreds of paper from the tissue roll often end up around the axes and can cause frictional heat that can ignite and cause a fire.
Firefly’s Unwinding fire protection solution will easily detect flames and effectively extinguish the fire. With a FD-UVIR flame detector on each side of the machine and water mist nozzles. The atomized drops are attracted to the base of the fire and are instantly converted into vapor, expanding its volume 1,700 times, thus displacing the oxygen required for combustion (without causing harm to operators).
This non-invasive suppression method generates a soft cooling effect, using very small amounts of water, avoiding, or significantly reducing damage to machinery, and preventing the fire from intensifying and spreading to other areas. It differs from conventional extinguishing methods because for example sprinklers, need large flames generating a high amount of heat to react and an extensive amount of water is needed to extinguish a fire.
Embosser and Rewinder
Embossing and winding machines, due to their function, generate considerable amounts of dry dust that accumulates around them and on their floor. The heat that they tend to generate by friction can ignite this accumulated dust and cause a fire.
Firefly’s protection solution, with two to five FD-UVIR flame detectors inside the embosser and winder, and water mist nozzles, effectively detects and extinguishes flames with a total time of seconds.
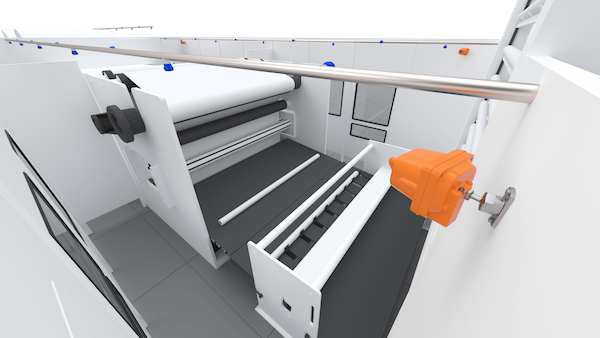
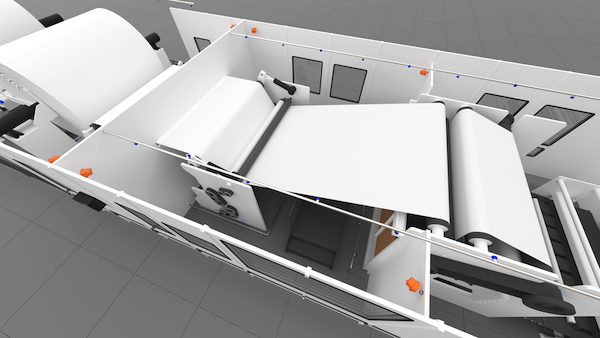
Log Saw, Band Saw and Napkin Folding
Fires in these types of enclosures or areas are unfortunately common and costly. Friction and or dangerous particles, including sparks generated during the sharpening of the saw blade can ignite the dust inside the Log saw, Band saw, or Napkin folding enclosure. As enclosures and areas are generally dusty, fires can easily cause equipment damage and production downtime.
Firefly’s Log saw, Band saw, or Napkin folding protection consists of extremely quick and automatic flame detection in combination with water mist suppression. With fast and automatic flame detection inside the enclosure, loss of production and equipment can be minimised. Water mist, compared to alternative suppression solutions such as CO2 or powder, is a non-invasive suppression method that will effectively suppress the potential dangers with a minimum effect on your production. When converted to vapor, water mist absorbs more heat than any other extinguishing agent.
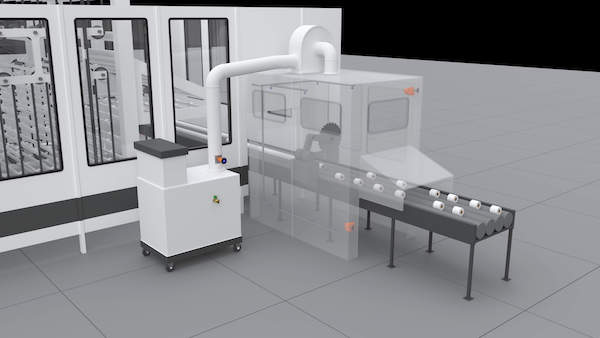
Dust Filters – Bag Houses
Ignition sources such as sparks, and hot particles generated in the tissue mill and the converting process can create fires and dust explosions in the dust extraction systems. It is therefore vital to also protect this part of your process.
Firefly’s dust extraction filter protection systems of spark and hot particles detectors with a temperature over 400°C (750°F), which is just below the ignition temperature for cellulose dust according to NFPA (National Fire Protection Association). At this temperature the particles are dark, they do not emit light, and Firefly has the only detectors in the world approved by FM Global to detect hot particles from 250°C and 400°C, thanks to its True IR technology.
A water spray extinguishing zone is typically installed downstream of the detectors to eliminate these dangerous particles from entering a filter or bag house.